A virtual sensor is ...
a revolutionary technology based on artificial intelligence that enables highly flexible collection of easily interpretable data from production
a method of integrating data from neural networks into existing IT or OT applications in manufacturing
a software application that transforms the digital image of production into interpretable data, enabling a digital twin of the manufacturing process
How it works
One or more cameras (VIS, IR, UWB) monitor the material and machines
A digital image of the monitored area is created from stored or live footage
A digital twin of a sensor is created on the virtual image, which converts the 2D or 3D model into measurements or objective quantitative evaluations of the situation, as a human would interpret from the digital image—for example, the percentage of a container filled, the condition of a mold, etc.
This general evaluation is performed by artificial intelligence at every moment of the recording, and the value is sent to the target system (e.g., existing MES, BI, PLM, etc.). The data stream can be handled like any other digital sensor stream translated into an IT protocol
A so-called detector can be installed on this sensor data, indicating the exact moment of an event relevant for decision-making, such as the start and end of a work cycle, the moment of material depletion, a forklift passing through an area, material placement, a specific setup step, and more
What can be detected using virtual sensors
Anyhing that can be observed with the naked eye:
Shape, color, position, size of an object
Position of a robotic arm, manipulator, press
Signal lights, dials, digital screens
Position and direction of movement of forklifts, cranes, vehicles
Fill level of containers, warehouse positions, bins

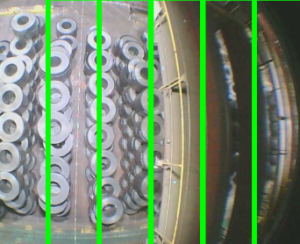

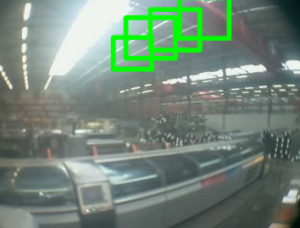
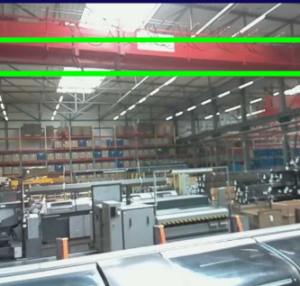
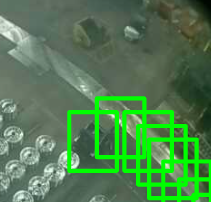
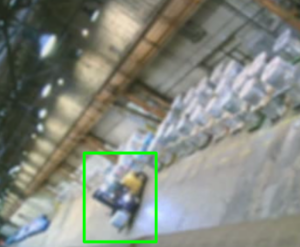
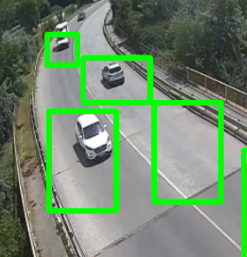
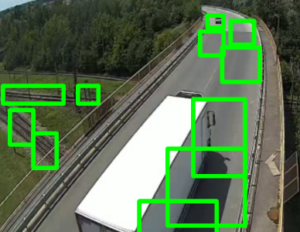
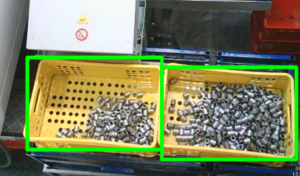
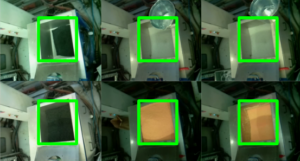
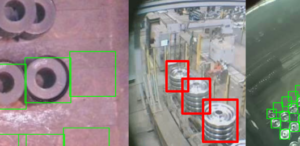
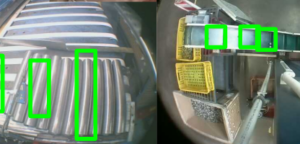
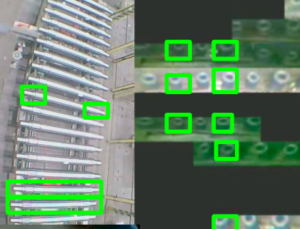

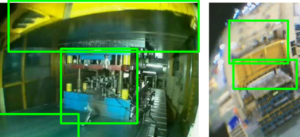
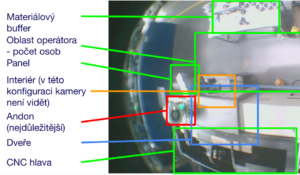
What is a dynamic virtual sensor
- A revolutionary technology that enables the instant deployment of highly reliable virtual sensors within seconds, without the need for large investments.
Currently, it is the only technology that allows the use of existing cameras in workshops or on production lines, along with standard computers, for immediate digitalization that pays for itself instantly.
It is a set of AI models that dynamically evolve over time through a system similar to variability escalation in the Toyota Production System.
How are virtual sensors by InovecTech better
We have mastered the DVS technology and offer enterprise solutions, digital twin modules, a platform that enables AI adoption with no new HW installation, and box solutions that enable a factory digitalization within 1 day. The optimization of the entire process—from hardware installation to monitoring sensor data from production—is so finely tuned using our human-in-the-loop AI technology that its performance (in terms of reliability, availability, and cost) far surpasses that of alternative hardware sensors or machine data collection in dozens of digitalization cases.
What advantages do virtual sensors by InovecTech give you?
The ability to install a sensor in the past
Installation speed – as fast as a few seconds per sensor if camera footage already exists
Data reliability – every signal is backed by an image that can be reviewed, allowing suspicious data to be selectively verified; falsifying the data is extremely difficult
Ease of interpretation – every signal is accompanied by an image that line workers can understand without needing knowledge of electronics or data analysis
Intuitive root cause analysis
Versatility – a single technology can collect data for dozens of use cases, as production is designed for visual inspection by humans to enable quick reactions
Scalability – it’s possible to install anywhere from a few to millions of virtual sensors very quickly, with minimal demand on plant electricians and no need to hire data scientists; standard interfaces for widely-used sensors enable the development of standardized solutions built on this data—more refined, more accessible, and more secure
Why is it revolutionary?
Since the introduction of the Industry 4.0 concept, a myth has spread that advanced analytics and artificial intelligence can improve manufacturing solely through OT data or IoT sensors. Factories are now drowning in data, with unrealistic expectations that data consultants will somehow extract valuable insights from terabytes of sensor signals.
The reasons for the failure of this approach are clear:
Data collected from the shop floor come from sources that were installed for specific purposes. It turns out that for slightly different purposes, this data is often unusable—for example, the sensor would need to be reoriented or placed in a different location.
Even when the desired insights are theoretically encoded in the data, a small change in hardware settings for data collection can invalidate a well-trained AI model. This effect is well known to radiologists, who, according to overly optimistic predictions, were supposed to be fully replaced by AI as early as 2021. However, AI only works reliably when fine-tuned, for example, specifically for a given CT scanner. Since IoT sensors used in manufacturing are highly diverse (often even custom-made), such fine-tuning is impractical.
It is highly likely that AI will replace all humans in manufacturing before it can fully solve this fundamentally unsolvable task by human means. That’s why past successes have been limited to replicating specific human abilities in a consistent and systematic way—for example, predictive maintenance of bearings or pistons based on machine sounds.
Virtual sensors follow this proven path. However, since entire factories are designed to be visually inspectable by humans, the potential of systems built on top of virtual sensors represents a true revolution.
How can virtual sensor output look like_
The data resembles outputs from standard IoT sensors—that is, a sensor value for each point in time. These values can be:
Viewed in our optimized web tool
Exported in table format (time – value) to a spreadsheet (Excel, Google Sheets, etc.)
Connected to a real-time monitoring tool
Sent to your database
Automatically inserted into your analytics / BI tool via a suitable interface
Integrated with our other data-driven production management tools
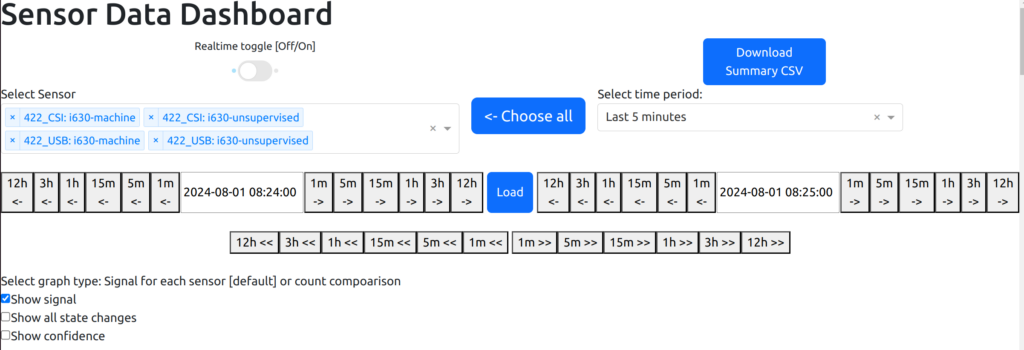
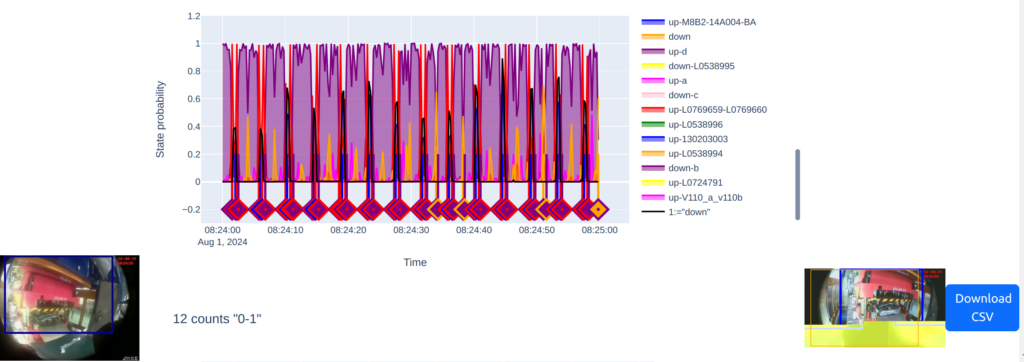
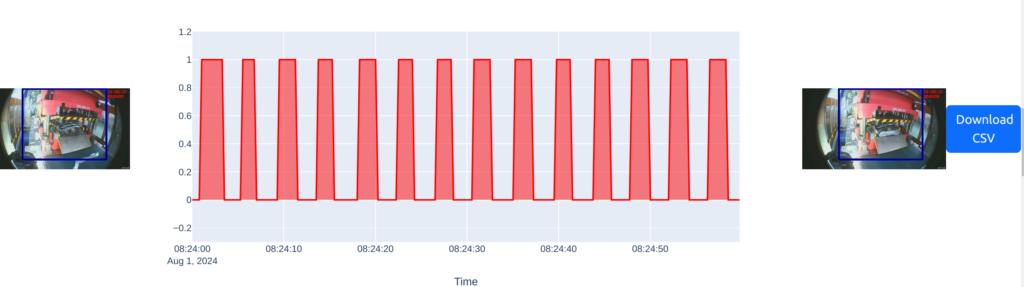
How to start with virtual sensors step by step:
The options are:
Do it yourself: If you already have a camera installed, data infrastructure in place, and neural networks deployed, you can build a data pipeline and run simple virtual sensors on your own or rented infrastructure. We recommend this approach only in exceptional cases—mainly if you have available internal IT capacity and the data being collected is of low priority, so there’s no need for sophisticated monitoring or error correction.
Reach out to your current IT providers: If they’re already our partners, you can simply arrange integration into new or existing projects at your facility.
Contact us directly: We’ll quickly schedule a short consultation, assess whether virtual sensors are suitable for your needs, and help connect you with a partner who can deliver the system.
The hardware infrastructure for virtual sensors can, in most cases, be available as soon as the next day. While this is also possible with hardware sensors, keep in mind that validating the data, interpreting it (and potentially designing the project or making physical modifications to production equipment) takes much longer—so the entire digitalization process is significantly faster with virtual sensors.